parts are important components of automobile, aircraft and mechanical equipment. Machining of mechanical parts can make the whole equipment more efficient, strong and able to play a role. In aircraft structure, in order to reduce the weight, a large number of aluminum alloy thin wall parts are used. Because of the large thermal expansion coefficient of the aluminum alloy parts, the thin-walled processing process is easy to be deformed, so it needs to be processed.
in fact, there are many reasons for the deformation of the aluminum alloy parts, which are related to the material, the shape of the parts, the production conditions and the performance of the cutting fluid. It mainly includes the following aspects: deformation caused by internal stress, cutting force, deformation caused by cutting heat and deformation caused by clamping force.
the material and geometric parameters of the tool have an important influence on the cutting force and the cutting heat. The correct choice of the cutting tool is very important to reduce the deformation of the parts.
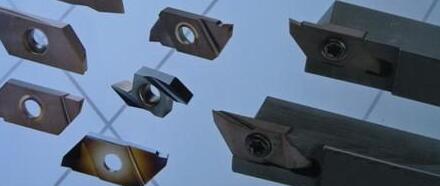
rational selection of tool geometric parameters.
front angle: under the condition of keeping the blade strength, the front angle is properly chosen, on the one hand, the sharp edge can be worn out. In addition, the cutting deformation can be reduced, the chip removal is smooth, and the cutting force and the cutting temperature can be reduced. Do not use the negative front angle tool.
rear corner: the size of the rear corner has a direct effect on the flank wear and the machined surface quality. The cutting thickness is an important condition for the selection of the rear angle. In rough milling, due to the large feed rate, heavy cutting load and high calorific value, the heat dissipation condition of the tool is required. Therefore, the rear corner should be selected a little. In precision milling, sharp edges are required to reduce the friction between the flank and the machined surface and reduce the elastic deformation. Therefore, the rear corner should be selected larger.
helix angle: to make milling stable and reduce milling force, the helix angle should be as large as possible.
main deflection angle: properly reducing the main deflection angle can improve the heat dissipation condition and reduce the average temperature of the processing area.